Downtime is costly and devastating to operations, leaving productivity and efficiency stagnation. As history has demonstrated, if one item ceases working or needs servicing within the production chain – even something as minor as cleaning – it can have substantial repercussions for the entire operation, so it is necessary to inspect program errors with specific services which became popular in internet-space and usually used by business owners to check website outage if they have problems with online-resources.
What to do
Instead of costly stockpiles to address downtime, a more prudent and efficient solution lies in the proactive management of potential disruptions. Web admins use this approach to prevent site problems – for example, Spectrum internet outage or system errors on other platforms. This method also allows production teams to plan and anticipate any issues that may arise while decreasing costs associated with maintaining extensive production inventories. Predictive maintenance is essential to avoid unexpected outages or delays and keep operations on track.
The difficulty is further exacerbated when dealing with thousands of individual parts that need to be monitored. Keeping comprehensive records and logs can prove daunting, and most asset management systems need to be equipped to signal which components may fail. Are you searching for a more straightforward way to keep your production lines running? With asset tagging and tracking, it is possible to predict when components will need replacing or repair. This allows engineers to take quick action, minimizing downtime while upgrading the faulty part.
Not only does this keep time, but it also saves money as more efficient processes are adopted that lead to improved outcomes. Technology related to asset tagging and tracking has been present for quite a while, yet it has progressed considerably in the past few years. Whereas only complete equipment used to be identified before, standard and custom components inside specific machines or pieces of equipment can be tagged too. This makes an immense difference.
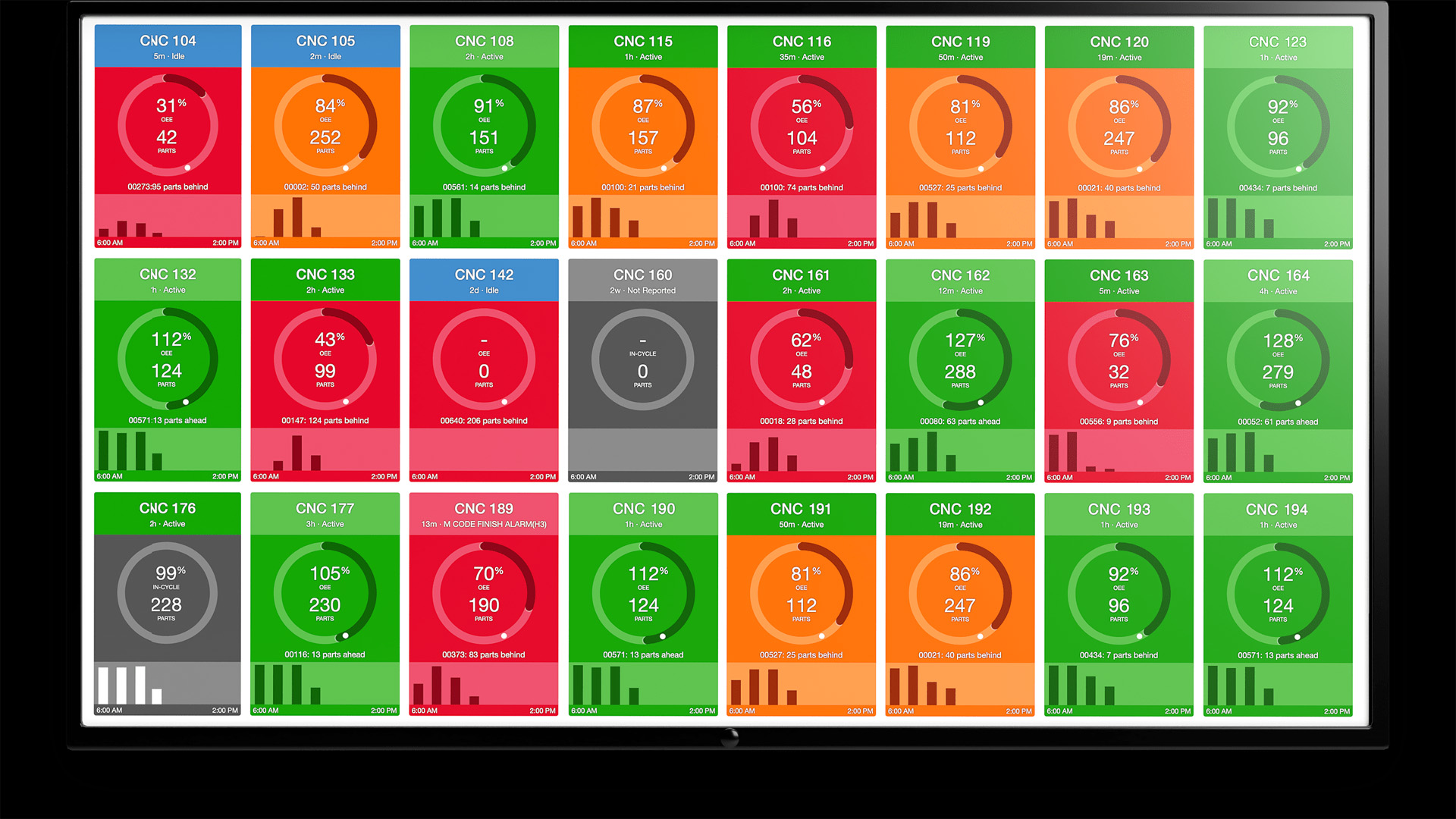
Helpful programs
One more game-changing feature is the capacity to monitor and trace a component utilizing an economical hand-held gadget such as a smartphone or tablet, onto which you can download an asset tracking platform application. But how does tagging work? Essentially, a label attached to any component created will contain an encoded barcode with all the essential details needed for that product.
This information could include its replacement parts history, specific maintenance and operations instructions (MRO), and a total bill of materials such as hoses, fittings, and other accessories. The tag can provide customized installation directions alongside lot numbers and further customizations.
In addition to being able to endure intense temperatures, UV light, salt spray, and other non-conductive conditions, as well as submersion in salt water or any fluid, the label may also carry essential information such as customer contact details, assembly date, system data, and environmental specifics.
The true benefit of this application is that all the above can happen virtually, with no need for costly and inconvenient downtime. In other words, being able to plan maintenance proactively allows machinery on the shop floor to remain in operation while awaiting a new part. This means minimal disruption when performing replacement work – drastically reducing typical delays experienced across factories.
With today’s cutthroat competition, uptime is paramount, so it’s wise to invest in modern web-based technology and mobile apps to eliminate lengthy downtimes.